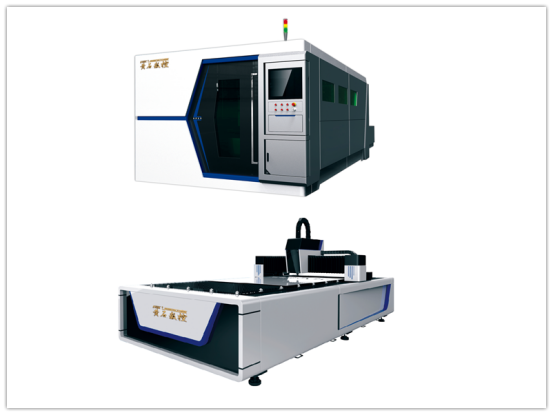
The application of metal laser cutting machine is very extensive, including many industries, and it is one of the necessary equipment for many companies, including advertising sign production (these are mainly stainless steel LOGO and logo cutting), sheet metal processing (sheet Metal processing basically includes all metal materials. These are generally bending, grinding, etc., and cutting is the most important process), chassis and cabinet production (in this regard, carbon steel or stainless steel is generally useful, but also mainly folding Bending and cutting 2 cutting processes), springs (belonging to the finishing process), subway parts, and the production of elevator casings, mechanical equipment casings, and kitchen utensils (mostly stainless steel), which surpass lasers The laser cutting machine setting of the company also participated in the production of the Seven Gods Eight Spacecraft, which actually involves various aspects. Widely used in sheet metal processing, advertising sign production, high and low voltage electrical cabinet production, mechanical parts, kitchenware, automobiles, machinery, metal crafts, saw blades, electrical parts, glasses industry, springs, circuit boards, electric kettles, medical micro Electronics, hardware, knife measuring tools and other industries.
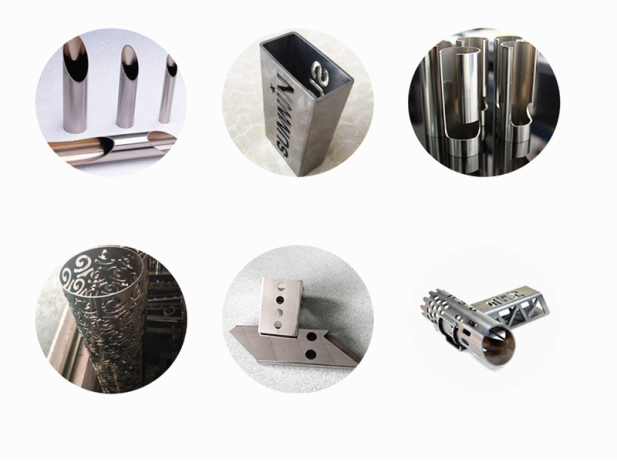
Quality
Cutting accuracy is the first element to judge the quality of a CNC laser cutting machine. Four factors affecting the cutting accuracy of CNC laser cutting machines:
1. The size of the laser agglomeration of the laser generator. If the light spot is very small after gathering, the cutting accuracy is very high, and the gap after cutting is also very small. It shows that the precision of the laser cutting machine is very high, and the quality is very high. However, the beam emitted by the laser is cone-shaped, so the slit cut out is also cone-shaped. Under this condition, the greater the thickness of the workpiece, the lower the accuracy, so the larger the slit.
2. The accuracy of the workbench. If the accuracy of the table is very high, the accuracy of cutting will also be improved. Therefore, the accuracy of the workbench is also a very important factor to measure the accuracy of the laser generator.
3. The laser beam is condensed into a cone. When cutting, the laser beam is tapered downwards. At this time, if the thickness of the cut workpiece is very large, the cutting accuracy will be reduced, and the cut gap will be very large.
4. Different cutting materials will also affect the accuracy of the laser cutting machine. Under the same circumstances, the accuracy of cutting stainless steel and aluminum will be very different, the cutting accuracy of stainless steel will be higher, and the cut surface will be smoother.
In summary, the quality of laser cutting can be measured by the following 6 standards:
1. Cutting surface roughness Rz
2. Cutting slag size
3. Cutting edge perpendicularity and slope u
4. Cutting edge round corner size r
5. Drag after stripes n
6. Flatness F
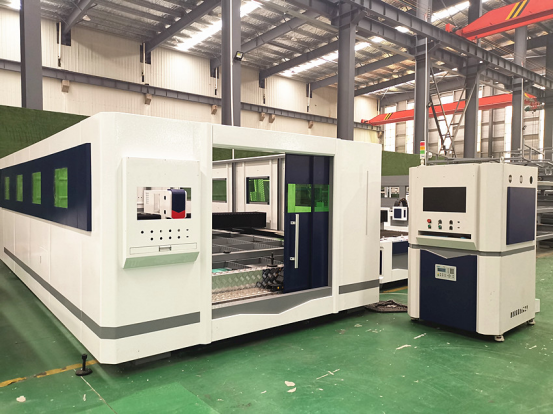