In shipbuilding, aircraft and other industries, there are often large metal parts forming requirements. At this time, it is necessary to use Double linkage cnc bending machine, Two bending machines work simultaneously to process large-size workpieces. The numerical control system controls the two bending machines synchronously, and currently only the expensive electro-hydraulic synchronous press brake and its numerical control system have such function. If the torsion axis bending machine can be used, the cost will drop even more.
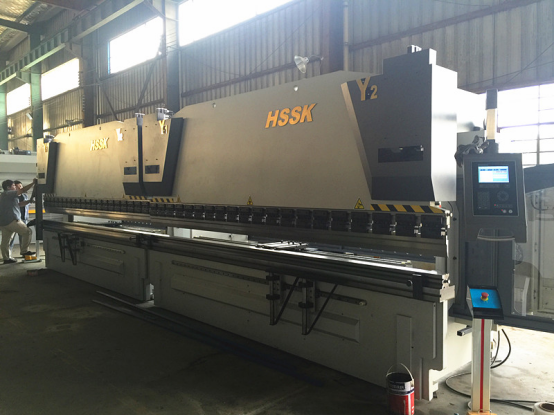

Machine features:
1. Generally use two press brakes of the same series and specifications, equipped with dual-machine linkage synchronization device.
2. All-steel welded structure is selected, vibration eliminates stress, and the machine has high strength and good rigidity.
3. The hydraulic system adopts the American special hydraulic system, which is simple, stable and reliable, and has a long life.
4. The synchronizing mechanism adopts machine-hydraulic servo and mechanical stopper, and is connected with the sliding block with a joint bearing. It has high synchronization and can accept a certain eccentric load, avoiding the damage of the synchronization organization caused by the eccentric load and the influence on the accuracy of the workpiece.
5. The slider stroke is adjusted by motor, LED digital display, and the display accuracy is 0.01 mm, which ensures the high-precision forming viewpoint of the sheet.
6. The backgauge distance is adjusted by motor, and the LED digital display is manually fine-tuned. The display accuracy can reach 0.01 mm, which eliminates the gap between the gears in the general digital display, and the display accuracy is high.
7. The slider stroke adjustment is an independent motorized organization, which has changed the previous cylinder internal adjustment, with high positioning accuracy, convenient repair, and prevented oil leakage and jamming of the cylinder caused by over-limit adjustment of the slider stroke.
8. The upper die is equipped with a deflection compensation organization, and a quick clamp organization is optional. The lower die deflection compensation equipment is installed for more than 250 tons, and the inclined block compensation or the oil cylinder compensation can be selected.
9. This machine is the latest equipment and belongs to the third generation of bending machine. The two machine tools can also be used separately at the same time, which improves production efficiency, high positioning accuracy, convenient repair, and beautiful appearance.

The key technology of dual-machine linkage is to adjust the speed of the two bending machines to synchronize, and to bend a workpiece at the same time to process a large workpiece. At present, the pressing speed of the torsion axis bending machine is not adjustable, so it is impossible to realize the dual-machine linkage operation with the torsion axis bending machine. It is precisely because of the structural and functional problems of the torsion axis bending machine and its numerical control system that it is technically difficult to use two torsion axis bending machines for dual-machine linkage.
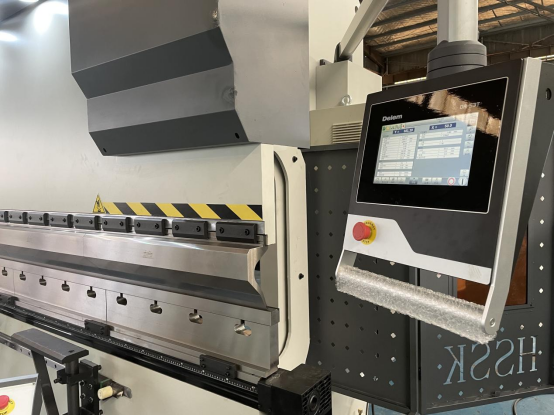
Technical solution
The technical problem to be solved by the two-machine linkage bending machine is to provide a control method to realize the linkage of the two bending machines. In order to solve this technical problem, we adopt the following technical solution: the dual-machine linkage bending machine includes two bending machines arranged side by side, each bending machine includes a frame, a slider, an upper die, a hydraulic drive system and a control system. The hydraulic drive system is controlled by the control system. The hydraulic drive system drives the slider, which drives the upper die to move up and down. The hydraulic drive system includes an oil tank, an oil pump, an electromagnetic pressure valve, a proportional flow valve and an oil cylinder. The oil outlet of the oil pump is connected to the oil inlet of the electromagnetic pressure valve, and the pressure oil port of the electromagnetic pressure valve is connected to the oil inlet of the proportional flow valve. The oil outlet of the proportional flow valve is connected to the cylinder; the two-machine linkage bending machine is also equipped with a detection device for measuring the position and speed of the upper die. The upper die detection device communicates with the control system to feedback the upper die press position to the control system And speed, the control systems of the two torsion axis bending machines realize synchronous control through synchronization signals.
Take the control system of one of the torsion axis bending machines as the host, and send a control signal to the control system of the other torsion axis bending machine, so that the control systems of the two torsion axis bending machines can realize synchronous control. When pressing, the upper die detection device feeds back the upper mold pressing position and speed to the control system, and the control system then controls the upper pinch die pressing speed to keep the upper die pressing position and speed of the two torsion axis press brake machines synchronized. The electric servo drive system includes a servo motor, a transmission device connecting the servo motor and the slider, and the servo motor drives the slider to move up and down through the transmission device. The transmission device includes a gear arranged on the output shaft of the servo motor and a rack arranged on the sliding block, and the gear and the rack mesh for transmission. The hydraulic drive system is provided with two oil cylinders, and the two oil cylinders are respectively arranged on the left and right sides of the frame. The piston rods of the oil cylinders are connected with the sliding block. The upper mold detection device is a grating ruler device.
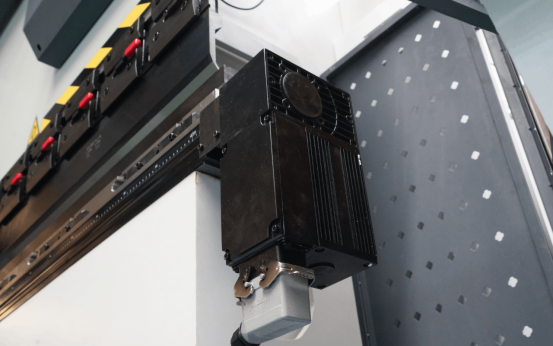
When the bending machine starts to work, the proportional flow valve is fully opened. When the upper die reaches the speed change point, the proportional flow valve starts to move. The control systems of the two torsion axis bending machines adjust the lower pressing speed of the upper die to make the two linked The lower pressing position and speed of the upper die of the torsion axis bending machine are kept synchronized. After the bending machine starts to work, the upper die is quickly lowered before the upper die reaches the speed change point. The control system issues a command to control the servo motor to rotate forward, and the servo motor controls the upper die to move down quickly until the upper die reaches the speed change point. After the bending is completed, when the upper die reaches the upper dead center, the upper die is fast-up phase, the control system sends instructions to control the servo motor to reverse, and the servo motor controls the upper module to move up quickly until the upper die reaches the upper dead center.
The dual-machine linkage system realizes synchronization control between the two control systems of the two linkage bending machines through a synchronization signal. At the same time, a proportional flow valve is added to the hydraulic drive system, and the lower pressure position of the upper mold is measured by the upper mold detection device. And speed, so that the two torsion axis bending machines can adjust the pressing speed of the upper die, that is, the pressing speed of the torsion axis bending machine can be adjusted through the controller. Therefore, the present invention can synchronize the speeds of the bending machines of the two bending machines, and simultaneously bend a workpiece, achieving the purpose of processing large workpieces.