Welding robots: one of the main categories of industrial robots, intelligence is the development trend.
Industrial robots are the most representative equipment for intelligent manufacturing, and their large-scale application is an important means to replace machines and improve production efficiency in the future manufacturing industry.
Welding robot is mainly composed of robot body and welding equipment. Robot body is mainly composed of six-axis robot arm and controller, its core components for the control system, reducer and servo motors, welding equipment, including welding power supply, special welding torch, automatic wire feeding device. In terms of structural differences, the traditional welding robot has a tutor, intelligent welding robot added a large number of software and sensors, without manual programming, adaptive adjustment of processing parameters and paths, without the need for a tutor.

Robotic laser automatic welding
Laser welding is a new type of laser welding, mainly for thin-walled materials, precision parts welding, can realize spot welding, butt welding, lap welding, stacking welding, angle welding, splicing welding, sealing welding and so on.
The self-developed single/double motor oscillating welding head can realize welding at any angle for all kinds of complicated welding seams and non-regular shapes of larger workpieces.
Laser welding machine saves about 80%-90% of electric energy, compared with arc welding, processing costs can be reduced by about 30%.
The operation of the equipment is simple and easy to learn, and the operator’s technical threshold is not high, which saves the labor cost.
Very low heat input, small deformation, smooth and beautiful weld seam, less welding follow-up treatment, reduce the labor cost of late polishing and leveling.
High weld quality, no porosity, can reduce and optimize the base material impurities, the organization can be refined after welding, weld strength, toughness at least equal to or even more than the base metal.
Precise control, small focusing point, high-precision positioning, easy to realize automation, and can realize the welding between certain dissimilar materials.
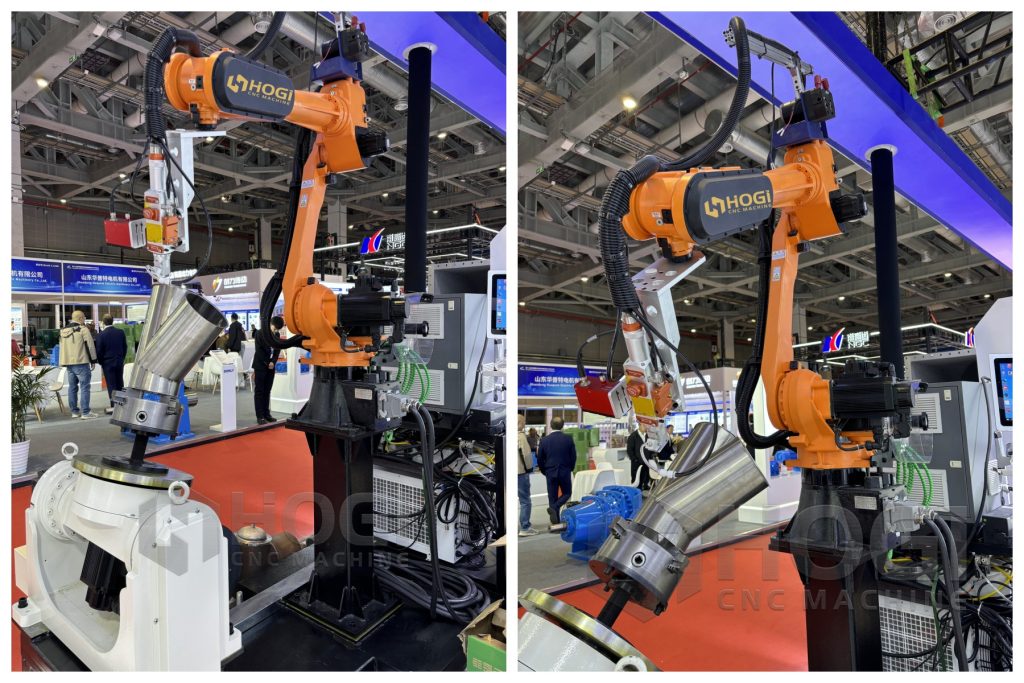
Laser welding robot welding advantages
Laser welding robot laser welding has the following unique advantages:
1. High efficiency: laser welding robot using contactless welding, can realize high-speed, high-quality welding, improve production efficiency and product qualification rate. Laser welding robots can work with computer numerical control systems or manipulators and robots to achieve automation and intelligent welding production.
2. High precision: laser welding robots use laser as a welding heat source, laser energy is highly concentrated, small heat-affected zone, small thermal deformation, which can realize precision processing. The laser welding robot can automatically identify and track the shape and position of the weld according to the shape and position of the weld to ensure the alignment accuracy and repeat positioning accuracy of the weld.
3. High quality: The laser welding robot can weld metals with high melting point, refractory and difficult to weld, such as titanium alloys and aluminum alloys, etc., and can realize welding between certain dissimilar materials. Laser welding robots have small weld joints, narrow weld seams, neat and beautiful appearance, no need or only simple post-processing. Laser welding robot’s weld seam organization is uniform, with fewer porosity and defects, which can reduce and optimize the base material impurities and improve the mechanical strength, corrosion resistance and electromagnetic properties of the weld seam.
4.High flexibility: laser welding robot is suitable for large format space welding, robot intelligent operation, flexible and reliable, can be six-axis linkage, can be any space welding, not limited to plane welding. Laser welding robot can be customized according to production requirements and fixtures to adapt to different specifications and shapes of the workpiece.
The difference between laser welding robots and normal welding
There are several differences between laser welding robot and ordinary welding:
1. The heat source is different. Laser welding robots use a laser beam with high energy density, which can heat the surface of the workpiece in a narrow area, causing it to melt or vaporize, forming a weld or notch. Ordinary welding uses arc, flame, resistance and other heat sources, need to contact the workpiece, producing a large amount of smoke, noise, radiation and other pollutants.
2. Different precision. Laser welding robot can realize tiny, precise, complex welding requirements, control the width, depth and shape of the weld, reduce deformation and defects, improve product performance and reliability. Ordinary welding is affected by the operator’s technical level and environmental conditions, prone to weld points are not secure, not beautiful, uneven and so on.
3. Different speeds. Laser welding robot can realize high-speed, continuous, automatic welding operations, improve productivity and quality, reduce costs and energy consumption. Ordinary welding requires manual operation, slower, less efficient, higher cost.
4. Flexibility is different. Laser welding robot can adapt to different materials, structures and shapes of welding, without direct contact with the workpiece, can be long-distance or difficult to reach parts of the welding, can realize multi-dimensional and multi-directional welding. Ordinary welding needs to be adjusted according to different workpieces and replacement equipment, less flexible.
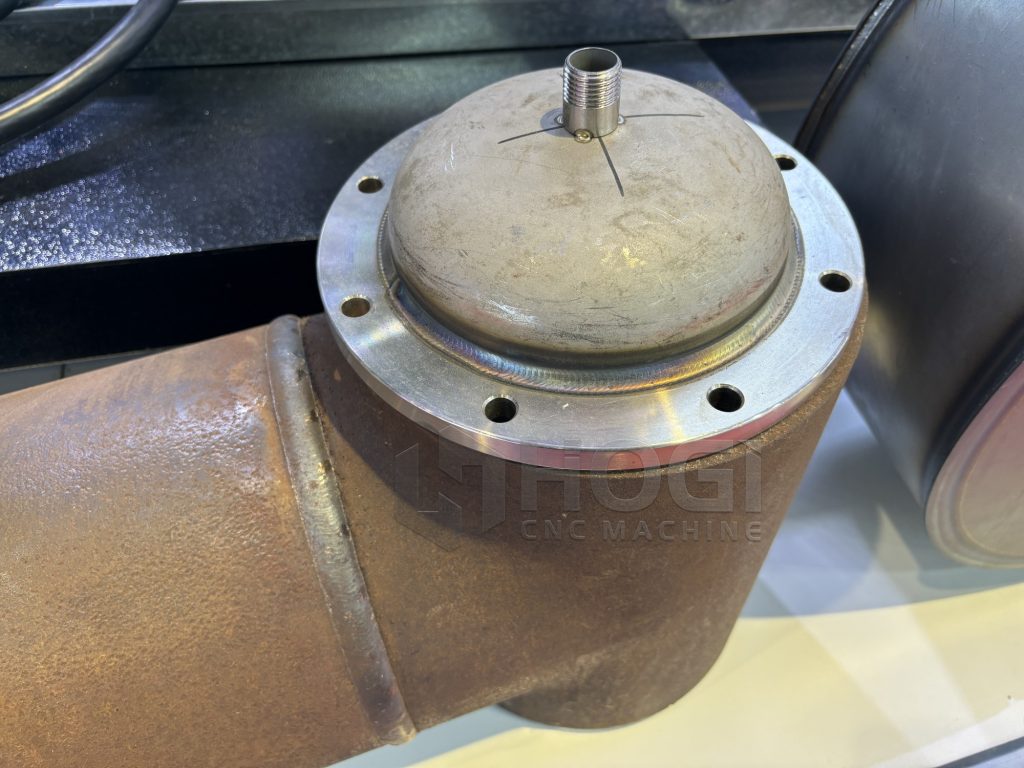