Sheet metal processing is the cutting or cold and hot forming of metal plates, profiles and pipes without changing their cross-sectional characteristics, and then assembly by welding, riveting and bolting, and finally manufacturing the required The processing methods of metal components mainly involve various professional work types such as fitter, blanking, stamping, metal cutting, welding, heat treatment, surface treatment, riveting, assembly and so on.
Characteristics of sheet metal processing technology.
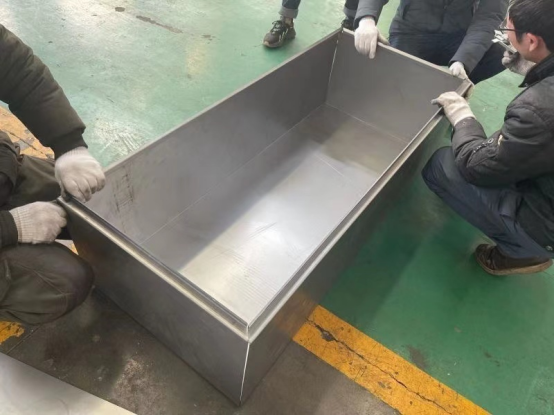
Sheet metal processing is mostly the processing of cold or hot separation and forming of raw materials without changing the cross-sectional characteristics of metal sheets, profiles, and pipes. Because the processed metal is plastically deformed below the recrystallization temperature, No chips are produced. Sheet metal processing can be used to make products of various shapes, sizes and properties, and the manufactured steel structure products have high strength and rigidity, and can make full use of their load-bearing capacity. In the sheet metal structure manufacturing process, the various parts that make up the structure can be assembled into components by welding, riveting, snapping, or expansion according to certain position, size relationship and accuracy requirements. Therefore, the design flexibility is large. . Based on the above analysis, sheet metal processing mainly has the following characteristics:
① Compared with the production and processing of forging and castings, sheet metal components have the advantages of light weight, saving metal materials, simple processing technology, reducing production costs, and saving production costs.
②Most of the welded sheet metal components have low processing accuracy and large welding deformation, so the post-weld deformation and correction amount are large.
③Due to the welded parts are non-detachable and difficult to repair, reasonable assembly methods and assembly procedures must be adopted to reduce or avoid waste. Large or extra-large products often need to be assembled on site, so trial assembly should be carried out in the factory first. It is advisable to temporarily replace the non-detachable connection with a detachable connection during trial installation.
④In the assembly process, it is often necessary to select, adjust, and repeatedly measure and inspect to ensure product quality.
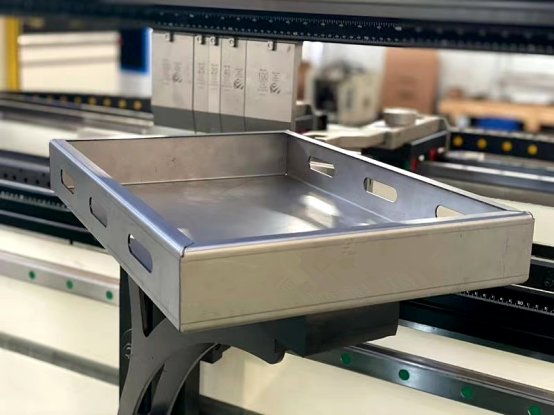