Spinning is a process that uses a rotating die and pressure to gradually deform metal sheets or tubes. During the process, the metal material is held on a rotating mandrel, and the spinning wheel applies pressure to the material along a specific trajectory, causing the material to conform to the shape of the mandrel under a combination of centrifugal force and pressure, thus molding the metal.

This process can be categorized into normal spinning and strong spinning. Ordinary spinning mainly changes the shape of the metal material with relatively small changes in thickness, while strong spinning causes the metal material to change significantly in the thickness direction, enabling the manufacture of more complex shapes and higher-strength parts.
The working principle of CNC spinning machine is to load the metal coil into the CNC spinning machine, then turn it to the position of the cutting die, and use the die to make the metal plate into the required shape. The CNC spinning machine has a high precision of cutting correction, can process different shapes, and has the advantage of fast cutting. In addition, CNC spinning machine adopts computer control technology, which can precisely control the working program, reduce human interference and improve production efficiency.
Principle of spinning process: Spinning non-cutting molding process is to make the metal round sheet blanks, cylinder blanks, prefabricated blanks into the rotating movement. A forming wheel is used to extrude the rotating billet and start the metal flowing. This process allows for the production of a wide range of hollow bodies with complex busbar shapes, small tolerance ranges, and excellent material properties and surface quality at minimal tooling costs. The spinning process allows for maximum accuracy in determining the wall thickness and profile of the workpiece, as well as accurate repeatability of the wall thickness and profile.
Advantages of spinning processing:
HIGH PRECISION: CNC spinning machine adopts advanced CNC technology and precise automatic control, which can realize high molding precision. It improves the quality and performance of products and meets various high precision processing needs. The motion trajectory of both the mold and the spinning wheel can be precisely controlled, making the dimensional error of the processed parts extremely small. Both complex surfaces and fine contours can meet the design requirements. CNC spinning machine adopts computer control technology, which can realize high precision processing quality.
High Material Utilization: Compared with some traditional metal machining processes, spinning does not produce large amounts of scrap. The metal material is gradually deformed during the spinning process, and almost no excess material is removed. CNC spinning machine has the advantage of fast cutting, which can improve the production efficiency. This is of great significance for saving costs and resources.
Automated production: CNC spinning machine has automated production capacity, which can realize automated control and processing through computer numerical control system. This can greatly improve production efficiency and processing speed, reduce labor costs and operating difficulties.
Good Mechanical Properties: Metal parts that have been spinning processed have an optimized internal metal fiber organization. This fiber organization is distributed along the shape of the part, resulting in an increase in both strength and toughness.
Processing a variety of materials: CNC spinning machine can process different shapes with versatility. CNC spinning machines can process a variety of metal materials, such as aluminum, copper, steel, etc., as well as non-metallic materials, such as plastics. This can meet the needs of a variety of different materials and improve processing efficiency and material utilization.
Strong flexibility: CNC spinning machine can realize the processing of many different shapes and sizes by modifying the program and replacing the molds. This can meet the needs of different users and improve the flexibility and adaptability of the equipment.
High efficiency and energy saving: CNC spinning machine adopts advanced CNC technology, which can realize high efficiency and energy saving processing. This can reduce energy consumption and production costs, which is in line with the requirements of sustainable development.
EASY MAINTENANCE: The CNC spinning machine adopts modular design, which is easy to maintain and repair.
In short: CNC spinning machine is a kind of efficient, high-precision and automatic processing equipment, which is widely used in various industries and fields. It can improve production efficiency and product quality, reduce production costs and energy consumption, and provide strong support for the sustainable development of enterprises.

CNC spinning machine processing in different fields:
Automotive field: Spinning process has an important application in automotive chassis processing. Some key parts of automobile chassis, such as wheel hubs and brake drums, need to have high strength and high precision. Spinning can produce parts to meet these requirements and improve the overall performance and safety of automobile chassis. At the same time, in other parts of the car, such as exhaust pipes and other metal parts with special shapes, can also be manufactured by spinning machining to improve the quality and performance of the car.
food processing equipment in the metal liner, etc.. Spinning processing can ensure the sealing and smoothness of these containers, and at the same time meet the food hygiene standards to ensure the safety of food in the processing and storage process.
Stage lighting: The design of stage lighting equipment often seeks unique shapes and high-quality light effects. Spinning can create a variety of creative shapes for stage lighting housings, lampshades and other components. The lampshade made by spinning processing can better control the scattering and reflection of light, creating a colorful stage lighting effects, bringing a visual feast for the audience.
Characteristics of the spin forming process include:
High molding precision. Spin forming process can make the metal plate or tube to achieve high precision forming, avoiding the defects such as deformation and cracks that may occur in the traditional stamping process.
High production efficiency. Spin molding process, only need to carry out a molding, while the traditional stamping needs to be formed several times, so spin molding can greatly improve production efficiency.
High material utilization. The spin forming process maximizes the use of metal materials because the sheet metal or pipe is formed only at the point of mold contact, leaving the rest of the sheet metal unaffected.
Wide range of application: Spin forming is suitable for all kinds of metal materials, including steel, aluminum, copper, stainless steel and so on.
The CNC spinning machine process can be divided into the following key steps:
Blank Preparation and Clamping: After pre-treatment, the metal coil or plate is fed into the working area of the CNC spinning machine. By means of a clamping device, the blank is firmly fixed to the mold, ensuring that no movement or deformation occurs during the process.
High-speed rotation of mold and blank: Driven by the CNC spinning machine, the mold and blank begin to rotate at a high speed. This rotation not only helps in uniform deformation of the material, but also improves the processing efficiency.
Continuous Extrusion of Forming Wheel: With the rotation of the die and the blank, the forming wheel starts to extrude the blank continuously from the radial direction. During this process, the CNC spinning machine continuously adjusts the position and pressure of the forming wheel through a precise control system to ensure that the blank is deformed according to a predetermined path and shape.
Plastic deformation of the material: The blank begins to deform plastically under the squeezing action of the forming wheel. This deformation is a process of flow and rearrangement of the metal, culminating in the formation of the desired thin-walled pipe or hollow rotary part.
Precision control and size detection: During the whole machining process, the CNC spinning machine monitors and adjusts the machining precision in real time through its built-in sensors and control system. At the same time, by matching the dimensional inspection device, it can ensure that the processed parts meet the design requirements.
No mold spinning process:
Principle of moldless spinning process: Moldless spinning refers to the molding process without a core mold inside the product, using the strength of the material itself to support the extrusion pressure exerted by the spinning wheel, and gradually achieve the preset molding effect. Therefore, the spinning process has high requirements for the equipment’s response speed, operational flexibility and functional reliability. The hardware configuration and functional structure of the equipment have a significant impact.
The sheet is mounted on the flange positioning axis, and the tail top is activated to press the sheet onto the end face of the simple mold to complete the sheet clamping.
Spinning series for wind turbines:
Spinning series for wind turbines: Main areas of application: ventilation, fans.
Advantages: simple tooling, generally only a simple convex mold, mold materials are cheap, can be used for ordinary cast iron or welded from sheet metal, simple processing, so low cost. After the spinning process, the mechanical strength of the material is significantly improved, so the wall thickness of the parts can be taken thinner, saving material. Can obtain no weld, beautiful appearance of the whole part. Spinning equipment is lightweight, low power consumption, but can process large parts, so it has the effect of investment and energy saving.
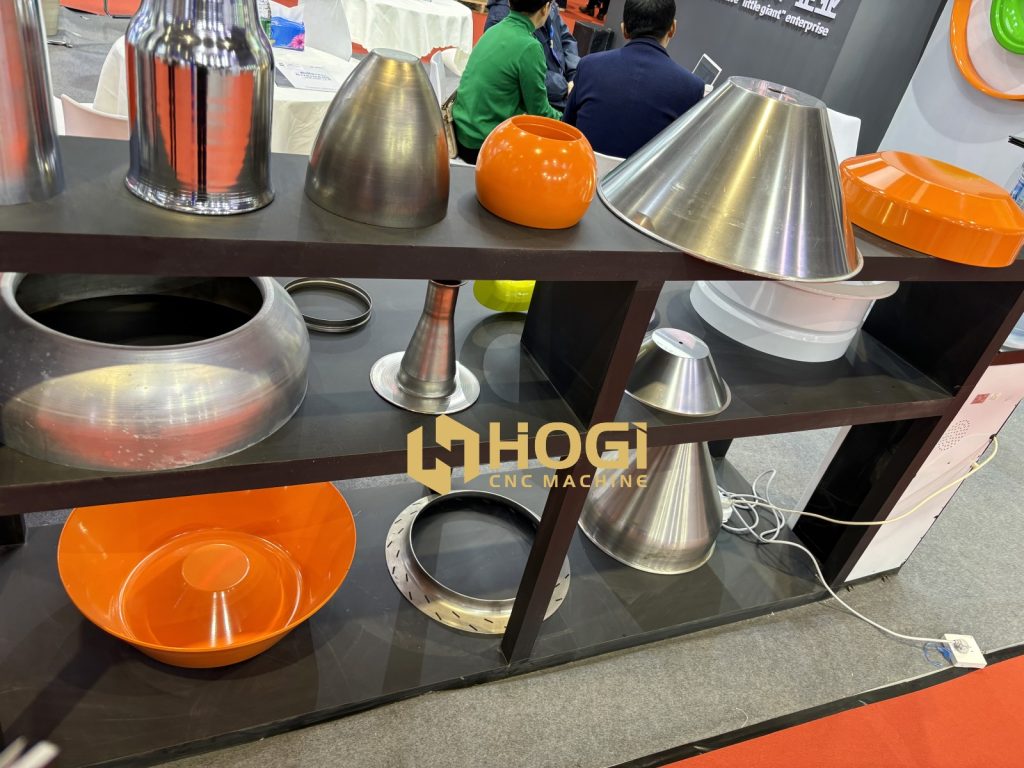