Stainless steel sinks can be seen everywhere in life,
Today, we will learn about the detailed sink production technology from plate purchase, processing to finished product assembly, and recommend suitable machines for everyone.
Procurement of sheet metal
●The overall thickness of the formed sink is uneven, and the thickness is usually about 0.7mm. The thickness of the steel plate commonly used in the better stainless steel sink is between 0.8mm and 1.5mm.
●The sink manufacturer buys steel plates of different widths according to the needs of different models of sinks, weighs the steel plates into coils, and then sends them to the sink manufacturer.
●Usually the maximum width of unprocessed steel plate is 1220mm, and the length is basically unlimited.

- Laser cutting:
The laser material cutting machine (figure attached 1) is the first process for making water tanks. The product shape is cut with a laser cutting machine. Generally, the water tank products are cross-shaped (figure attached 2), and the power 1500w-3000w models are used for cutting .
There are two ways to open the sink: 1. The cross-shaped material is cut completely, which is convenient and simple. 2. Cut square materials of different sizes and splice them into a cross shape.
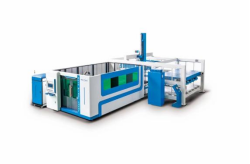
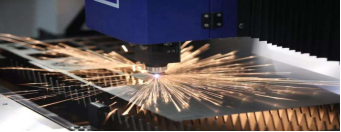
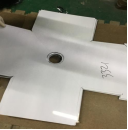
- 2.Pressure flow line pressure flow water hole:
The water hole under the sink is a drainage hole, which is formed by punching machine (Figure 1), and press water line is formed by right-angle tool of bending machine. The whole process is convenient and simple.
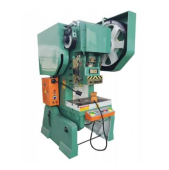

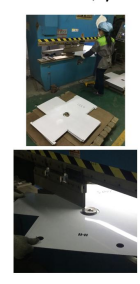
bending
3.The bending machine is to bend the cross-shaped material to form, which is convenient for subsequent processing. It is formed by a conventional 100-ton hydraulic bending machine, and the configuration of the CNC system can reduce the error
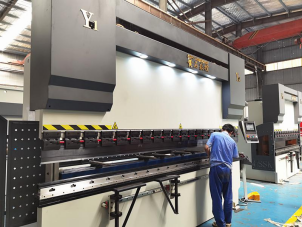
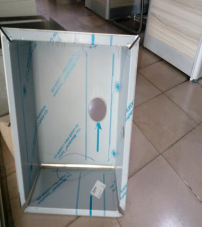
- Right Angle Welding Machine
After the sink is bent and formed, the head is fixed by manual spot welding to make it easy to weld straight lines. The right-angle welding machine adopts a touch screen system, which is stable and convenient. You can customize the welding method according to the needs of semi-melting or full-melting.
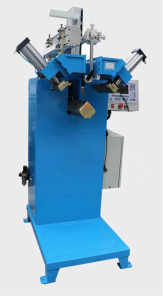

- Special machine for pressing seam, special machine for pressing angle
After bending and forming, the initial process of the arc water tank is to first press the welding seam and the bottom corner of the water tank. This is a shaping process before welding, which is convenient for welding, so that the manufactured water tank is not only beautiful, but also improves the quality of the product.
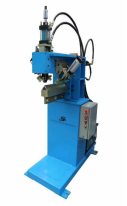
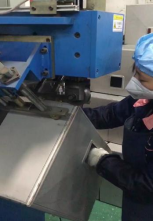
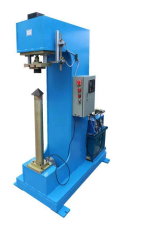
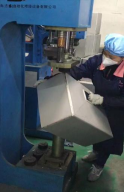
- 6.Semicircle press sewing machine
(Flanging sink or sink with plate) press seam treatment, direct pressure type backward rolling press seam weld, the operation process is convenient, and it is very quick to get started. Convenient welding and polishing after pressure seam bead
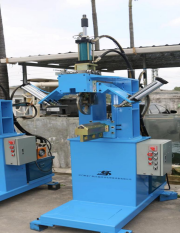
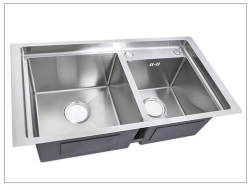
- 7.Special welding machine for fillet sink
After shaping, the sink products are welded. This welding equipment is CNC operated and programmed welding. The whole welding process is smooth and smooth. Pay special attention to the need for a windless environment so as not to affect the welding effect.
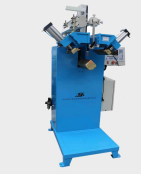
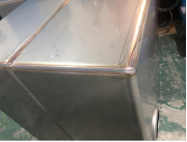
- 8.CNC plane welding machine
The flat welding of the water tank is the direct connection between the thick material panel and the tank liner, and the fusion is carried out by CNC drawing welding. The entire welding bead is flat and smooth, which is convenient for subsequent processing and polishing. The CNC programming program product can be used for any flat welding. The operation process is convenient and concise.
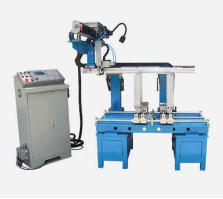
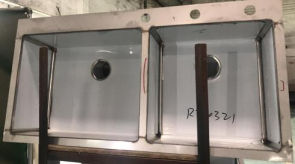
- 9.Horizontal grinding machine
The welded product has welding traces at the arc angle position, which needs to be polished and polished. Through adjustable and repeated extension, the welding traces can be completely processed.
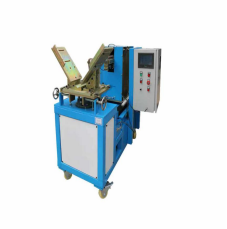
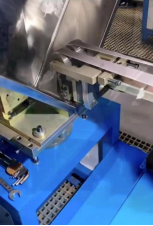
- 10. External grinder for sink welding
This machine is currently a special commercial sink in China. Some sink products also need to be polished to polish the welding marks on the outside of the arc corners.
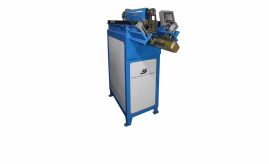
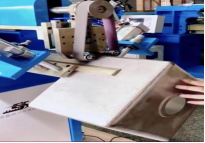
10. Flat wire drawing machine for sink panel, Automatic Polishing machine,Flat wire drawing and polishing
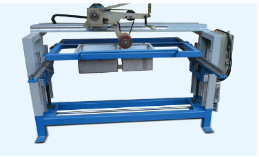
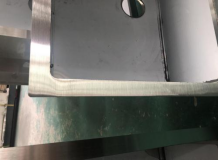
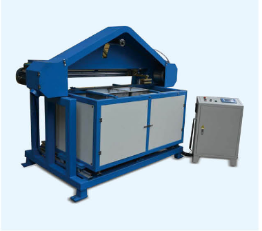
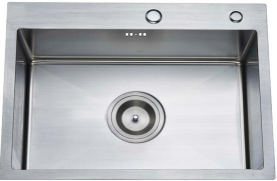