The machine adopts advanced numerical control system and novel design; it has the characteristics of high processing precision, simple operation, no noise and no vibration.
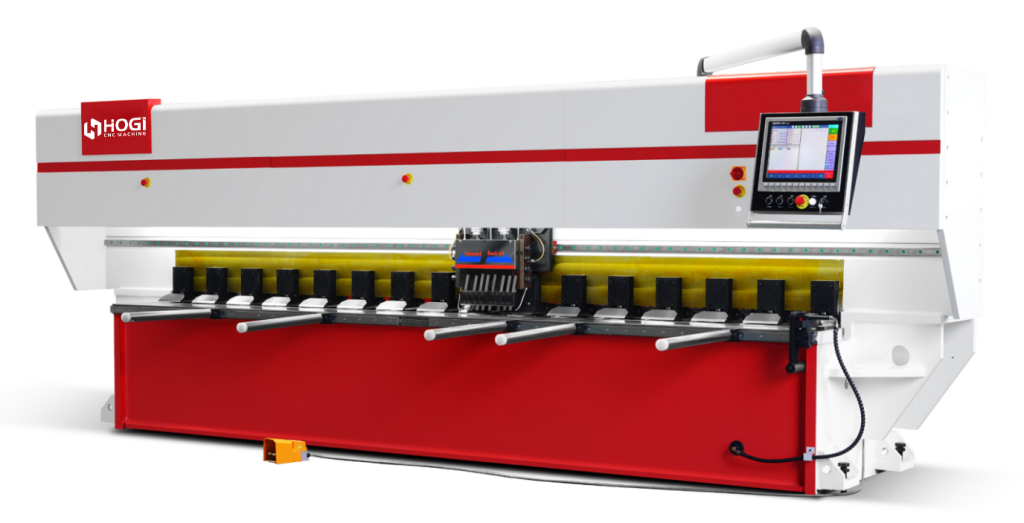
Usage description
Horizontal full-servo CNC v grooving machine is often used for processing sheet metal workpieces (including stainless steel plate, aluminum plate, aluminum-plastic plate, copper plate, iron plate, bakelite board, acrylic plate and some other special plates), which can be V-grooved on the plate , U-shaped groove and other irregular groove processing, especially suitable for V-shaped groove processing before bending of sheet metal workpiece.

Performance characteristics
1.The horizontal full servo CNC sheet metal v grooving machine is an upgraded product researched and developed by HOGI engineers on the basis of the Korean horizontal sheet metal v slotting machine. This machine has all the performance of the traditional horizontal machine, which can fully solve the customer’s actual A series of problems encountered during operation. Based on the products of horizontal slotting machines at home and abroad, a 4-axis full servo design is used, which has made an essential breakthrough.
2.The appearance structure adopts steel plate welding technology, which has strong shock resistance; internal stress is eliminated by tempering and has good stability; the machine is sandblasted to remove rust and sprayed with anti-rust paint. The whole machine is processed on the CNC horizontal v groove machine, so that the whole machine can ensure the parallelism and perpendicularity of each installation surface.
3.The platform type double guide rail structure is adopted, the beam runs more smoothly, and the tool post processes the plate by moving left and right and back and forth, which can ensure the accuracy of each part of the groove depth.
4.The processing technology of four forming knives enables even cutting of each blade during processing.
5.Adopt full hydraulic or pneumatic clamping and pressing, work fast and at the same time make the processed products have no clamping marks or indentations, and the whole processing process has the function of blowing up and cooling.
6.Adopt high-speed precision rack and pinion, precision ball screw and high precision linear guide. The main shaft system is driven by a high torque main shaft servo motor with imported planetary reducer. Makes the tool post more stable and faster when processing the workpiece.
7.The worktable adopts high-strength low-alloy steel plate as the base surface, so that the worktable is not easy to be worn when processing the workpiece. The machine also has a self-planing function.
8.The horizontal full-servo CNC v groove machine adopts CNC numerical control, which is easy to learn and understand by the operator and accurate positioning.
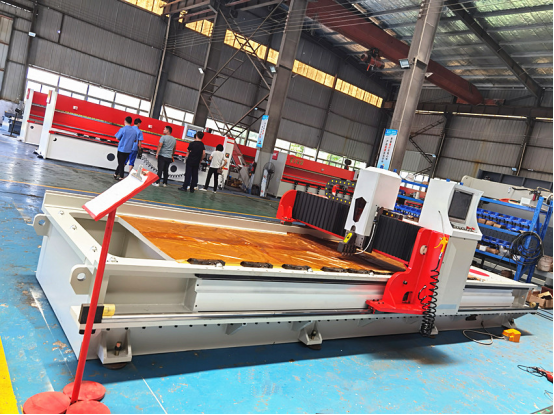
Structure introduction
- Crossbeam shaft system: It is composed of main motor 5.5KW AC spindle servo motor, 1:5 star reducer timing belt, synchronization wheel, high-precision rack and pinion, linear guide and other components. Its function is that the servo motor drives the precision gear through the planetary reducer to drive the tool holder to move linearly on the linear guide to provide power for planing.
- Y1, Y2 axis system: It is composed of 1KW AC servo motor, synchronous belt, synchronous wheel, ball screw, movable clamp and other parts. Its function is that the motor drives the ball screw with power to move linearly on the linear guide to achieve accurate positioning of the processed V groove.
- Z-axis system: It is composed of 1KW AC servo motor, precision coupling, ball screw, dovetail guide rail and tool holder. Its function is that the motor drives the tool holder to move linearly by driving the ball screw to provide precise positioning of the tool holder mechanism.
- Hydraulic system: They are a fixed pressing system, a mobile clamping system and a set of air blowing cooling systems. The two sets of hydraulic systems and one set of air blowing are controlled by the system through electrical appliances.
- Electrical control system: It is composed of Easycat special v cutting machine system, driver, electrical control components, electrical board and other accessories. The electrical board is installed inside the machine for easy maintenance and strong protection. Various tasks of this equipment can be realized through system control.
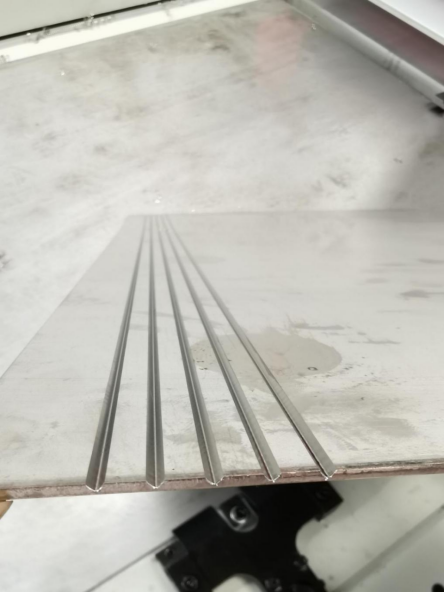
Maintenance
- Regularly check whether the fasteners are loose. If there is any looseness, tighten them in time after confirming the correct position.
- Before daily use, it is necessary to add lithium-based grease to each transmission part, and to add N320 lubricant to the surface of each linear guide and ball screw to protect the transmission mechanism of the slotting machine.
- When using the slotting machine, pay attention to the temperature and the sound of each transmission part. If there is any abnormal sound, stop it in time to avoid serious damage.
- Frequently check whether the grounding of the machine is good, whether the wire insulation is good, and a protective conduit must be added outside the wire.
- The slotting machine is composed of four groups of servo motor drive systems. It has functions such as overload and short circuit protection. To ensure the safety of electrical equipment. The machine must be grounded safely and reliably before use. The control components are installed in the electrical cabinet, and the processing operation of the workpiece is completed through the touch screen control. The structure is simple and the operation is convenient.